|

Zinc coatings
for iron and steel provide excellent corrosion resistance
in most atmospheres, in hard fresh waters, and in
contact with many natural and synthetic substances.
Zinc coatings are widely used to protect finished
products ranging from structural steelwork for buildings
and bridges, to nuts, bolts, strip, sheet, wire and
tube. The electrochemical relationship between zinc
and steel enables zinc coatings also to protect steel
at cut edges and at breaks in the coating by a sacrificial
action. (See also Zinc anodes: cathodic protection) |
The
following are the seven principal methods
of applying zinc
coatings:
Individual
steel components or fabrications are chemically
cleaned by acid to remove rust and millscale
before being immersed in a bath of molten
zinc at about 450°C. In the galvanizing
bath
a series of zinc-iron alloy layers are
formed
by a metallurgical reaction between the
iron
and zinc. As the steel is withdrawn, a
layer
of molten zinc remains on the surface.
The metallurgical bond
between the base steel and the coating
means that in addition to excellent corrosion
resistance hot dip galvanized coatings
are much less susceptible to handling damage
than other coatings such as paint systems.
Applications include structural steelwork,
lampposts, crash barriers, power transmission
towers, railway electrification supports,
security fencing, trailers and many others.
Galvanizing offers duel protection against rust. Firstly, the coating covers
the whole surface, reaching into even the most awkward corners of complicated
structures, and provides an impermeable barrier between the basis material
and the atmosphere which corrodes at a much slower rate than steel. Secondly,
because of its electrochemical properties, zinc will sacrificially protect
any small areas of damage and the coating may even self heal. Even when the
exposed area is too wide to allow self-healing, these properties prevent the
sideways creep of rust beneath the zinc coating.
After several preparatory stages, clean, non-oxidised steel strip is passed
at high speed through a molten zinc alloy bath, wiped to control the coating
thickness and cooled to form a thin, continuous zinc (or zinc alloy) coating.
Depending on the final use, various thermal or chemical treatments may be applied.
Continuous paint or plastic coatings may also be applied at the production
plant to provide additional protection and/or a coloured finish. Applications
include roofing and cladding for industrial and commercial buildings, domestic
appliances and automotive bodies. All car manufacturers now use steel strip
that has either been continuously hot dip galvanized or zinc plated.
Atomised
particles of molten zinc are projected
on to a grit-blasted
steel surface from a special flame or arc
pistol fed with zinc or zinc alloy wire.
The process is often applied to structural
components too large to be dipped in a
galvanizing bath, and to structures which
are likely to distort during hot dip galvanizing.
The zinc coating is electrodeposited onto prepared steel from a solution of
zinc salts. The process is used to protect smaller articles - such as nuts,
bolts and other fasteners and small pressings – which require a finer
finish than galvanizing can normally provide, although the coating is thinner.
The process has also been adapted to provide thin coatings on steel strip and
wire.
Prepared iron or steel articles are heated with zinc dust and sand in a slowly
rotating drum at a temperature just below the melting point of zinc until
the zinc has formed a zinc-iron alloy coating over their surfaces. The coating
is very even, matt-grey in appearance and is mainly used for fairly small
articles because of the difficulty of heating the contents of large drums
evenly.
These are paints in which very high levels of fine zinc dust have been incorporated.
Because of the very high pigmentation with zinc particles , the dry film is
electrically conductive and so acts to some degree as a metallic coating. Zinc
dust paints can be applied to any rust and scale-free steel surface by brushing,
spraying or dipping. They are mainly used to protect factory steel work, ship’s
hulls and parts of car bodies and also to repair damage to other types of zinc
coatings.
Automatic grit blasting
and zinc dust paint spraying equipment
are widely used in steel workshops and
shipyards to protect steel plates during
storage before fabrication and until application
of the final coating system.
Steel articles
are cleaned and then given a very thin
coating of copper by immersion in a copper
sulphate solution. Zinc is then impacted
onto the surface by tumbling with a mixture
of zinc dust and ballotini (the tiny glass
beads that are used in reflective paints)
in an aqueous medium. A thin even coating
is formed. The treatments are carried out
at room temperature so there is no risk
of softening tempered steel articles such
as springs |
|
Pressure die casting,
is a fast economical process for mass producing
accurate parts. Molten metal is forced under pressure
into permanent steel dies which are opened mechanically
to allow the casting to be ejected. When specially
developed zinc alloys - based on zinc of at least
99.99% purity, with additions of aluminium, magnesium
and sometimes copper - are cast using the hot chamber
variant of this process, the resulting parts can
be not only uniquely accurate but also strong and
with excellent corrosion resistance. When required
for functional or aesthetic reasons, zinc die castings
can accept a wide range of surface finishes including
plating, painting and plastic coating.
Given this combination of strength, accuracy, consistency and finishability,
it is not surprising that zinc alloy die castings are used in a vast range of
applications: in car manufacture for handles, locks, carburettors, fuel pumps,
etc.; in domestic appliances; for locks, door handles, bathroom fittings and
other items of builder’s hardware; and in a variety of other products including
scale model toys and zip fasteners.
|
|
In
addition to the pressure die casting alloys there
are three alloys containing approximately 8, 12
and 27% aluminium that are used for traditional
sand castings or gravity die castings. With their
relatively low melting points and competitive mechanical
properties, they can be sometimes be used as alternatives
to aluminium, cast iron or brass, thus saving energy
and production time. Exceptional fluidity allows
thin wall castings to be made when required. If
needed, secondary finishing operations like machining
are easy and heat treatments are rarely required.
A zinc alloy containing of
30% aluminium and 5% per cent copper (known in
the United Kingdom as Alzen 305) can be used to
replace phosphor bronze in some bearing applications,
particularly for high loads and low speeds. This
alloy can also be extruded.
Zinc alloys based on 22% aluminium
display marked superplasticity at 260°C after preparatory
heat treatment. In sheet form they can be vacuum
of blow-moulded in cheap dies, taking advantage
of the 1000 per cent elongation available. These
alloys have found niche markets, particularly replacing
other sheet metal in equipment housings. |
|
Brasses
are copper-zinc alloys with a zinc content ranging
from about 20 to 40%, and sometimes containing
additions of other metals. Alpha brasses with 28
to 37% zinc content are single-phase alloys suitable
for cold working (i.e. rolling, pressing and drawing),
and for small castings. The alpha-beta brasses
with 40 to 45% zinc content consist of two phases
and are suitable for casting, hot pressing and
extrusion.
Brasses are easily recognised
by their yellow colour and – because of
their ease of working, high corrosion resistance
and good electrical conductivity – are
widely used in a wide range of engineering applications
as well as for plumbing and electrical components.
For further information on brass visit Copper
Development Association on www.brass.org. |
|
Zinc oxide is the most important compound of zinc. It is an indispensable raw
material for a multitude of everyday products and is produced in a number of
different 'grades' of purity and particle size depending where it is to be used.
Zinc oxide is made by heating
zinc metal or residues containing metallic zinc
to temperatures beyond the boiling point of
907°C.
The zinc vaporises and is allowed contact with
the
air:
it oxidises
and is cooled, collected and graded.
Glass and ceramics: zinc
oxide is a fluxing agent in the preparation of
frits and enamels for ceramic wall and floor
tiles.
Rubber and tyre products: zinc oxide is essential. It is an activator in
the vulcanisation process, putting the 'bounce'
into the rubber. Other benefits include improved
physical properties and resistance to degradation.
Electronics: high purity
grades of zinc oxide are used in specialised
applications such as ferrites and in varistors
to protect sensitive equipment from electrical
power surges.
Pharmaceuticals and cosmetics: for example suntan lotions (to absorb ultraviolet
radiation), baby creams and antiseptic healing creams.
Nutrition: zinc is an essential
micronutrient for plants and animals and humans.
Zinc oxide is a convenient form in which to add
zinc to fertilisers and animal feeds to avoid
deficiency. It is also used in the preparation
of other zinc compounds used in the preparation
of dietary supplements for humans |
|
As for zinc oxide,
zinc dust is made by vaporising metallic zinc.
However the vapour is in this case allowed to condense
in the absence of air, when it forms a fine powder.
The
principal uses of zinc dust are in paints and
sherardising (See under
Zinc Coatings). It is also used in alkaline batteries
and as a chemical reducing agent
|
|
Zinc
phosphate is essentially produced by reacting
zinc oxide with phosphoric acid, followed by
precipitation, filtration and drying. It is available
as a product in various states of hydration.
Zinc phosphate is mainly used in solvent or water-borne
anti-corrosive primer systems and paints.
|
|
The
main use of rolled zinc sheet and strip is for
roofing, cladding, flashings, and rainwater disposal
applications. It has been used extensively for
these purposes in continental Europe for many years.
Now, with increased awareness of its technical
and aesthetic qualities, its use is rapidly increasing
in the UK.
The product is used today
is a zinc–copper-titanium alloy. This conforms
to a European standard – EN 988, which
covers such factors as surface finish, dimensional
tolerances, tensile and creep strength.
In addition to its technical
qualities zinc sheet offers the advantages of
excellent visual appearance, long life with minimal
maintenance, cost effectiveness, and a versatility
which enables it to be used confidently for innovative
architectural designs.
Whilst the main tonnage of
zinc sheet is used for architectural purposes
it has a wide range of other applications, including
electrical and engineering components, printing,
organ pipes, coffin linings, gaskets, stencils,
bar and table tops, with new uses continually
being developed.
|
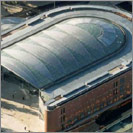 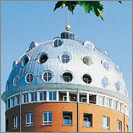
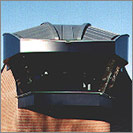 |
Because
of their different positions in the electrochemical
series, when zinc and iron or steel are joined
together and placed in an electrolyte, a cell
is formed in which the zinc becomes the anode and the steel the cathode.
The zinc then dissolves preferentially ('sacrifices') and the steel does
not rust. This is the process that enables zinc coatings to protect steel
at damaged areas (See 'Zinc coatings')
Marine sacrificial
zinc anodes, which are available in many shapes
and sizes, are bolted onto ships’ hulls
and ballast tanks, rigs and other installations
to protect the steel structure from corrosion.
High purity zinc and a range of special alloys
are used for cathodic protection to ensure
that the surface remains active. |
|
|
|
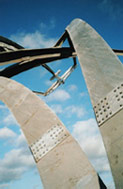 |